Sensors
We have to cover a few things before we can just start checking sensors. What are the kinds of sensors and how they work? What is a sensor? Quickly, it's a devise that checks a mechanical value and converts it into an electrical signal. Don't confuse a sensor with a switch. At times we call (my self included) inputs sensors, but this isn't true. Some inputs have an ON state and OFF state, these are called switches. Switches come ON at a set value and do not indicate an actual value, simply greater or lesser than its switching level.
Blah, Blah, moving on. An important note we must cover now is that the EEC operates a majority of the sensors at 5-volts DC. Huh? Yes 5-volts, the alternator and batteries are not dependable for voltage supply when it comes to sensitive electronics. The automotive electrical system ranges from 10-14 volts on an average day. Inside EEC is a voltage regulator, this steps the voltage down to a constant 5-volts. This voltage is called Reference Voltage. The sensors are supplied with this Reference Voltage and the sensor returns a variable amount of this to the EEC to indicate the status of the system the sensors is watching.
Some of the sensors need a special ground to get rid of the left over Reference Voltage that isn't sent to the EEC as a status. The EEC also provides a 5-volt ground loop for these select sensors. This special ground is called Signal Return. Lets quickly explain how this all works. The EEC sends a 5-volt Reference Voltage to a sensor; the sensor sends 1.87 volts back to the EEC as the sensor status, and the rest of the voltage (which should be 3.13-volts) down the Signal Return.
Now that I've told you how accurate the sensors are, let's mention how versatile the sensor system is. The ECC has programming that admits not all sensors are created equal. Once you have installed a new sensor you then re-attach the battery, you disconnected it right? You should have, and not just to protect against arcs, the EEC's Keep-Alive memory stores the sensor irregularities. Sensors are not all manufactured the same; there is a 15% tolerance from one sensor to the next one rolling off the assembly line. Once you re-connect the battery the KAM reads all the sensor baselines and stores these as "normal". It's kind'a like an aerial picture of all the EFI system components. The EEC can now plug in a sensor reading compared to baseline for an accurate value. If the sensor (over time) starts to loss its sensitivity, the EEC will catch on (from its original memory) and begin to compensate for this. As the sensor ages and it's readings get worse a fault code will be stored in the KAM memory. When trouble shooting a problem, always check for codes prior to disconnecting the battery, which erases the codes stored in the KAM memory. Then any codes next time will be after your last repair.
Now you have an idea of how the sensors and EEC communicate with each other. Click on the name or picture of the sensor below, from there you will learn more about each sensor and how to confirm it is operating correctly.
Stator
This sensor tells the computer engine rotation. It sits under the distributor cap and picks up a signal from a wheel with teeth. The wheel has the same number of teeth as cylinders in the engine. The #1 cylinder tooth is smaller to identify firing order. This is the most important sensor. Without it working properly the computer never senses the engine moving and the entire vehicle is a paper weight.
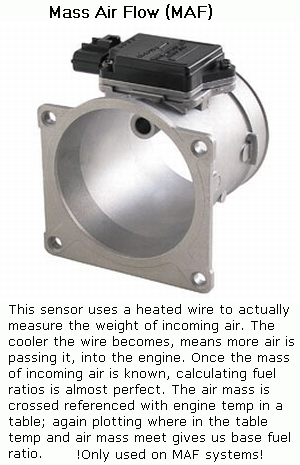
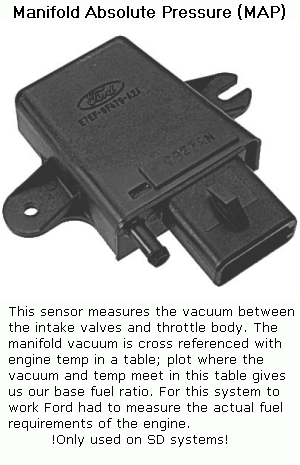
Throttle Position Sensor (TPS)
Self explanatory, it measures how far you push the skinny pedal. This tells the computer how aggressively we want to drive, the computer is programmed to enrich fuel mixtures the further the throttle is opened. Just like an accelerator pump in a carburetor. Programming also alters the timing more aggressively to match. This sensor is very important in clueing the computer to future events, as it responds quicker to driver changes than any other sensor.
Engine Coolant Temperature (ECT)
This measures the temperature of engine, and has a great impact on fuel ratio. This makes simple work of enriching the mixture on start up, overheating, and full throttle fun. It also allows us to lean out the mixture at certain times, to shorten the time it takes to warm up the engine helping us get great fuel economy.
Air Charge Temp sensor (ACT)
This measures the temperature of the air entering the engine. Which impacts the fuel ratio; the cooler the incoming air is the denser it is. Denser air can utilize more fuel, giving us even greater accuracy in obtaining our desired air to fuel ratio.
Heated Exhaust Gas Oxygen sensor (HEGO)
This sensor measures the oxygen content in the exhaust gas. This sensor is for feedback, it tells the computer when the air to fuel ratio is above or below 14.7:1. Sometimes the computer is attempting this mixture and sometimes it ignores the HEGO. For more, please seek further reading on the web or in books.
Barometric Pressure sensor (BP)
This sensor measures the pressure of the outside air. This allows you to drive from Death Valley, California to Denver, Colorado. Keeping fuel ratios perfect for each elevation along the trip. This is something carburetors could never do. Speed density systems re-use the MAP sensor to obtain this data prior to start up.
Vehicle Speed Sensor (VSS)
Self explanatory, it tells the computer how fast you are going. This allows certain emissions functions to be operated while on the highway. Also effects fuel delivery during deceleration.
Knock Sensor (KS)
The knock sensor is used to detect engine detonation or spark knock. As a result, a voltage sent to the PCM which will retard spark timing.
EGR Valve Position sensor (EVP)
This sensor mounted to the Exhaust Gas Recirculation Valve (EGR) monitors its position. The computer delivers less fuel and more spark timing when the EGR is open. Lowering fuel millage and tail pipe emissions.